Sludge special drum drying system
Key words
Category
Enquiry
Parameter download
Rotary drum drying process
Waste heat air or heat exchange air enters the rotary dryer and directly exchanges heat and mass with wet sludge in the channel. It is equipped with a special crushing device (specially designed structure) to quickly evaporate the water in the sludge. The smaller sludge particles are discharged from the dryer and collected together with the gas through the outer channel, while the larger sludge particles stay in the dryer for a longer time until drying is completed. Part of the exhaust gas is extracted and treated by a deodorizer to meet atmospheric emission standards (or cooled by water foam dust removal) before being discharged into the atmosphere.
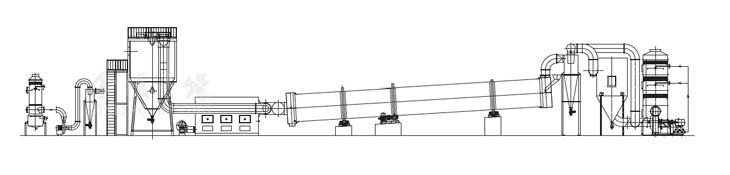
Key technological innovation points
(1) According to the characteristics and status of the sludge drying process, different dispersion and crushing devices are used in sections to greatly improve the drying efficiency.
(2) Using special sealing materials to ensure sealing effect and greatly improve service life
(3) The bearing adopts a cooling device to reduce the operating temperature of the bearing and extend its service life;
(4) Indirect heating can be used to reduce exhaust air volume and improve heat utilization efficiency:
(5) Adopt different sheet cutting forms according to different states of materials to reduce the degree of bonding;
(6) Adopt different feeding methods based on material characteristics to prevent blockage of the feed.
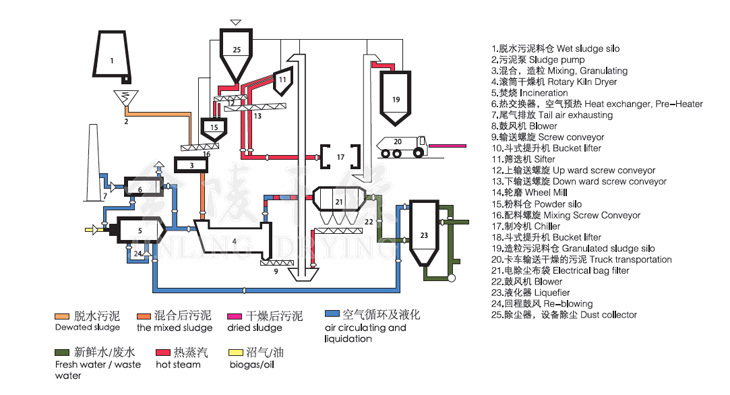
Performance parameters of drum sludge dryer (reference)
Dry conditions | Feed moisture content% | 80 | |||||
Discharge moisture content% | 40 | ||||||
Material outlet temperature ℃ | 90 | ||||||
Inlet air temperature (with hot blast stove)℃ | 500 | ||||||
Air outlet temperature ℃ | 100~130 | ||||||
Material data | Feeding amount t/d | 50 | 100 | 200 | |||
Water evaporation ratet/d | ~33 | ~66 | ~132 | ||||
Discharge quantity t/d | ~17 | ~68 | ~68 | ||||
Equipment model | ø1500×12000 | ø2000×16000 | ø2800×20000 | ||||
Installed power kw/h | ~70 | ~110 | ~200 | ||||
Overall dimensions of the host (reference) mm | 24000×3500×5500 | 34000×4000×6500 | 44000×5000×8500 |
Related Equipment
Leave your needs behind
We will contact you within one working day. Please pay attention to your email.